About Us
The University of Minnesota Solar Vehicle Project (UMNSVP) was founded by a group of ambitious undergraduate students in 1990. By 1993, our first solar car, Aurora I, was built. The team has built 14 vehicles in total. We are one of the most decorated teams in America, having raced in over 30 different solar challenges on 3 different continents. Our 14th car, Freya, is the winner of the 2022 American Solar Challenge MOV Class. Read more about each of our cars here.
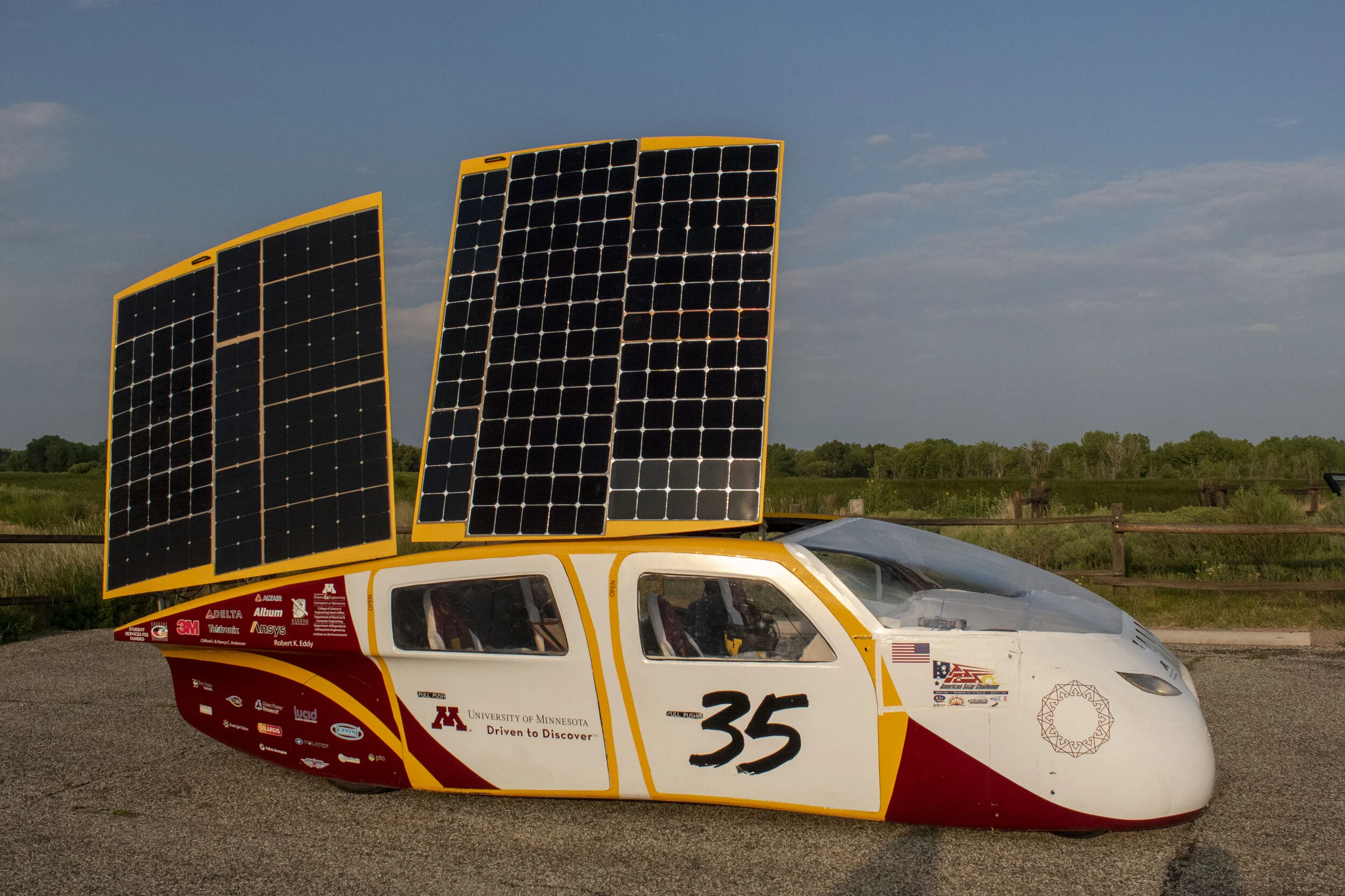